The Scientific Research Behind Porosity: A Comprehensive Overview for Welders and Fabricators
Comprehending the elaborate systems behind porosity in welding is crucial for welders and makers pursuing flawless craftsmanship. As metalworkers explore the midsts of this phenomenon, they reveal a world governed by numerous elements that influence the formation of these minuscule voids within welds. From the structure of the base materials to the intricacies of the welding process itself, a wide variety of variables conspire to either worsen or reduce the existence of porosity. In this comprehensive overview, we will unravel the scientific research behind porosity, discovering its impacts on weld top quality and unveiling progressed methods for its control. Join us on this journey through the microcosm of welding blemishes, where precision satisfies understanding in the search of remarkable welds.
Understanding Porosity in Welding
FIRST SENTENCE:
Examination of porosity in welding exposes critical insights right into the integrity and high quality of the weld joint. Porosity, identified by the presence of tooth cavities or gaps within the weld steel, is a common worry in welding procedures. These voids, if not correctly resolved, can compromise the architectural honesty and mechanical residential properties of the weld, leading to prospective failings in the ended up item.
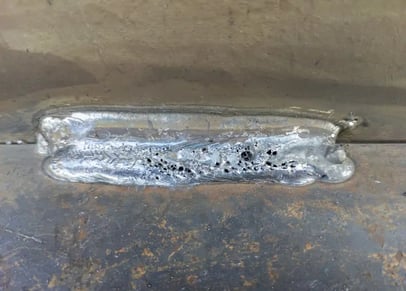
To spot and quantify porosity, non-destructive testing methods such as ultrasonic screening or X-ray evaluation are frequently utilized. These methods permit for the identification of internal issues without jeopardizing the honesty of the weld. By assessing the size, form, and distribution of porosity within a weld, welders can make educated choices to enhance their welding processes and accomplish sounder weld joints.
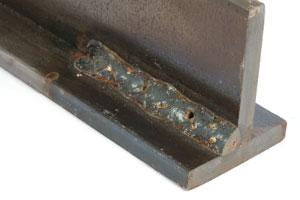
Variables Influencing Porosity Formation
The occurrence of porosity in welding is influenced by a myriad of variables, varying from gas protecting performance to the intricacies of welding specification setups. Welding parameters, consisting of voltage, present, take a trip speed, and electrode type, also influence porosity formation. The welding technique employed, such as gas metal arc welding (GMAW) or shielded metal arc welding (SMAW), can affect porosity formation due to variations in warmth circulation and gas protection - What is Porosity.
Impacts of Porosity on Weld High Quality
Porosity formation considerably jeopardizes the structural stability and mechanical buildings of welded joints. When porosity exists in a weld, it produces gaps or cavities within the product, decreasing the overall stamina of the joint. These voids function as anxiety focus factors, making the weld much more vulnerable to splitting and failing under lots. The visibility of porosity likewise deteriorates the weld's resistance to rust, as the trapped air or gases within the voids can respond with the surrounding setting, causing deterioration in time. In addition, porosity can impede the weld's capacity to withstand stress or influence, additional endangering the overall quality and dependability of the welded structure. In critical applications such as aerospace, auto, or structural buildings, where safety and toughness are paramount, the destructive effects of porosity on weld quality can have extreme consequences, stressing the relevance of decreasing porosity with appropriate welding methods and treatments.
Methods to Decrease Porosity
In addition, using the proper welding parameters, such as the proper voltage, current, and travel rate, is essential in avoiding porosity. Keeping a consistent arc size and angle during welding likewise helps minimize the probability article of porosity.

Making use of the appropriate welding method, such as back-stepping or utilizing a weaving movement, can likewise assist disperse warm uniformly and decrease the opportunities of porosity formation. By implementing these techniques, welders can successfully reduce porosity and generate high-grade welded joints.

Advanced Solutions for Porosity Control
Implementing innovative innovations and cutting-edge methods plays a crucial duty in accomplishing premium control over porosity in welding procedures. One sophisticated option is using sophisticated gas mixes. Protecting gases like helium or a combination of argon and hydrogen can help in reducing porosity by providing much better arc stability and boosted gas insurance coverage. Get More Info Furthermore, utilizing innovative welding methods such as pulsed MIG welding or modified environment welding can additionally assist reduce porosity concerns.
Another advanced service includes the use of advanced welding equipment. Making use of tools with built-in features like waveform control and advanced power resources can enhance weld quality and reduce porosity threats. Moreover, the execution of automated welding systems with specific control over parameters can significantly minimize porosity problems.
In addition, including sophisticated surveillance and evaluation innovations such as see here now real-time X-ray imaging or automated ultrasonic testing can aid in discovering porosity early in the welding process, enabling instant corrective activities. On the whole, incorporating these sophisticated services can considerably boost porosity control and enhance the total top quality of welded elements.
Conclusion
To conclude, recognizing the science behind porosity in welding is crucial for welders and makers to generate premium welds. By recognizing the elements affecting porosity formation and carrying out strategies to lessen it, welders can boost the general weld high quality. Advanced remedies for porosity control can additionally enhance the welding procedure and make sure a strong and reliable weld. It is necessary for welders to continually enlighten themselves on porosity and carry out finest methods to achieve optimum results.
Comments on “Comprehensive Guide: What is Porosity in Welding and Exactly How to avoid It”